Isolation of Polluting Equipment & Systems- The isolation of polluting equipment and systems involves physically separating them from the rest of the facility to contain potential pollution and minimize its impact on the environment. This can be achieved through various methods, including:
- Physical Barriers: Enclosing the polluting equipment within a sealed chamber or room. This prevents the release of pollutants into the surrounding environment.Opens in a new windowoizom.com Physical Barriers for Isolation of Polluting Equipment & Systems
- Ventilation Systems: Installing specialized ventilation systems to capture and remove pollutants from the isolated area. These systems can be equipped with filters or scrubbers to clean the air before it is released back into the atmosphere.Opens in a new windowwww.systech-design.com Ventilation Systems for Isolation of Polluting Equipment & Systems
- Containment: Using specialized materials or techniques to prevent the spread of pollutants. This can include the use of containment mats, spill kits, or secondary containment structures.Opens in a new windowzips.com Containment for Isolation of Polluting Equipment & Systems
- Remote Operation: Controlling the polluting equipment from a remote location to minimize exposure to pollutants and reduce the risk of accidents.Opens in a new windowwww.mdpi.com Remote Operation for Isolation of Polluting Equipment & Systems
The specific method of isolation will depend on the type of pollution, the equipment involved, and the regulatory requirements. However, the goal is always to minimize the environmental impact of the polluting equipment and systems while ensuring the safety of workers and the public.
What is Required Isolation of Polluting Equipment & Systems
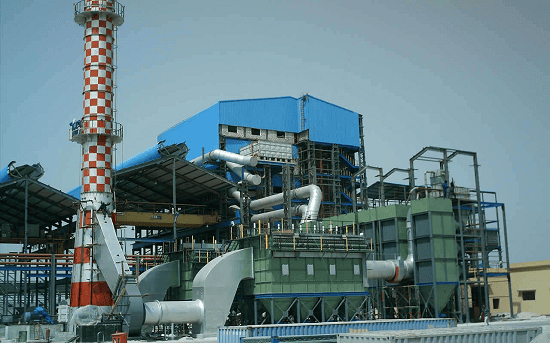
The required isolation of polluting equipment and systems depends on several factors, including:
- Type of Pollution: The nature and severity of the pollution will determine the level of isolation required. For example, highly toxic or hazardous materials will require more stringent isolation measures than less harmful pollutants.Opens in a new windowoizom.com Type of Pollution for Isolation of Polluting Equipment & Systems
- Regulatory Requirements: Environmental regulations and industry standards will dictate the minimum level of isolation required to comply with legal and safety requirements.Opens in a new windowehs.princeton.edu Regulatory Requirements for Isolation of Polluting Equipment & Systems
- Environmental Impact: The potential impact of the pollution on the surrounding environment will influence the level of isolation needed to protect ecosystems and human health.Opens in a new windowwww.mdpi.com Environmental Impact for Isolation of Polluting Equipment & Systems
- Risk Assessment: A thorough risk assessment will identify potential hazards and determine the appropriate level of isolation to mitigate those risks.Opens in a new windowwww.protectuk.police.uk Risk Assessment for Isolation of Polluting Equipment & Systems
In general, the required isolation of polluting equipment and systems should be sufficient to:
- Prevent the release of pollutants into the environment.
- Protect human health and safety.
- Comply with all applicable regulations and standards.
- Minimize the environmental impact of the polluting equipment and systems.
The specific requirements for isolation will vary depending on the individual circumstances. However, it is important to consult with environmental experts and regulatory agencies to ensure that the isolation measures are adequate and effective.
Who is Required Isolation of Polluting Equipment & Systems
Courtesy: HYBIZTV HD
The entities required to isolate polluting equipment and systems can vary depending on the specific regulations and the nature of the industry. However, some common examples include:
- Industrial Facilities: Manufacturing plants, power plants, and other industrial facilities that generate pollution are often required to isolate polluting equipment and systems to comply with environmental regulations.Opens in a new windowoizom.com Industrial Facilities for Isolation of Polluting Equipment & Systems
- Waste Management Facilities: Facilities that handle hazardous waste or other types of waste are required to isolate polluting equipment and systems to prevent the release of pollutants into the environment.Opens in a new windowwww.mdpi.com Waste Management Facilities for Isolation of Polluting Equipment & Systems
- Research Laboratories: Laboratories that handle hazardous chemicals or conduct experiments that generate pollution may be required to isolate polluting equipment and systems to protect researchers and the environment.Opens in a new windowwww.systech-design.com Research Laboratories for Isolation of Polluting Equipment & Systems
- Construction Sites: Construction sites may be required to isolate polluting equipment and systems to prevent the release of dust, debris, and other pollutants into the surrounding environment. Opens in a new windowsitemate.com Construction Sites for Isolation of Polluting Equipment & Systems
In general, any entity that operates equipment or systems that have the potential to generate pollution may be required to implement isolation measures to comply with environmental regulations and protect public health and safety. It is important to consult with relevant regulatory agencies and environmental experts to determine the specific requirements for isolation in a particular situation.
When is Required Isolation of Polluting Equipment & Systems
The required isolation of polluting equipment and systems is typically necessary:
- During Operation: When the equipment is actively running and generating pollution.Opens in a new windowwww.iqsdirectory.com Isolation of Polluting Equipment & Systems During Operation
- During Maintenance or Repair: When the equipment is being serviced or repaired, there is a risk of accidental release of pollutants.Opens in a new windowrradar.com Isolation of Polluting Equipment & Systems During Maintenance or Repair
- During Decommissioning: When the equipment is being retired or dismantled, there is a potential for the release of hazardous materials or pollutants. Opens in a new windowwww.esimtech.com Isolation of Polluting Equipment & Systems During Decommissioning
- In Case of Emergencies: In the event of an accident or other emergency, isolation measures may be necessary to contain the release of pollutants and prevent further harm.Opens in a new windowaaqr.org Isolation of Polluting Equipment & Systems In Case of Emergencies
The specific timing and duration of isolation will depend on the nature of the pollution, the equipment involved, and the regulatory requirements. However, it is important to implement isolation measures whenever there is a risk of pollution release to protect human health, safety, and the environment.
Where is Required Isolation of Polluting Equipment & Systems
The required isolation of polluting equipment and systems can occur in various locations, depending on the specific circumstances:
- Dedicated Isolation Rooms or Chambers: These are specifically designed areas to house polluting equipment, providing a controlled environment to contain emissions.Opens in a new windowwww.hepacart.com Dedicated Isolation Rooms or Chambers for Isolation of Polluting Equipment & Systems
- Within Existing Facilities: Isolation can be achieved within existing buildings or structures by creating designated areas or using physical barriers to separate polluting equipment from other operations.Opens in a new windowwww.iqsdirectory.com Isolation of Polluting Equipment & Systems Within Existing Facilities
- Outdoor Enclosures: For some types of equipment, outdoor enclosures or shelters may be used to isolate them and control emissions.Opens in a new windowwww.delvallebox.com Outdoor Enclosures for Isolation of Polluting Equipment & Systems
- Underground Facilities: In some cases, underground facilities may be used to isolate particularly hazardous or polluting equipment.Opens in a new windowwww.mdpi.com Underground Facilities for Isolation of Polluting Equipment & Systems
The specific location for isolation will depend on factors such as the type of pollution, the size and complexity of the equipment, and the available space and resources. The goal is always to choose a location that provides adequate containment and minimizes the risk of pollution release.
How is Required Isolation of Polluting Equipment & Systems
Courtesy: Fair Engineering Company
The isolation of polluting equipment and systems can be achieved through various methods, including:
- Physical Barriers: Enclosing the polluting equipment within a sealed chamber or room. This prevents the release of pollutants into the surrounding environment.Opens in a new windowoizom.com Physical Barriers for Isolation of Polluting Equipment & Systems
- Ventilation Systems: Installing specialized ventilation systems to capture and remove pollutants from the isolated area. These systems can be equipped with filters or scrubbers to clean the air before it is released back into the atmosphere. Opens in a new windowwww.systech-design.com Ventilation Systems for Isolation of Polluting Equipment & Systems
- Containment: Using specialized materials or techniques to prevent the spread of pollutants. This can include the use of containment mats, spill kits, or secondary containment structures.Opens in a new windowzips.com Containment for Isolation of Polluting Equipment & Systems
- Remote Operation: Controlling the polluting equipment from a remote location to minimize exposure to pollutants and reduce the risk of accidents.Opens in a new windowwww.mdpi.com Remote Operation for Isolation of Polluting Equipment & Systems
The specific method of isolation will depend on the type of pollution, the equipment involved, and the regulatory requirements. However, the goal is always to minimize the environmental impact of the polluting equipment and systems while ensuring the safety of workers and the public.
Case Study on Isolation of Polluting Equipment & Systems
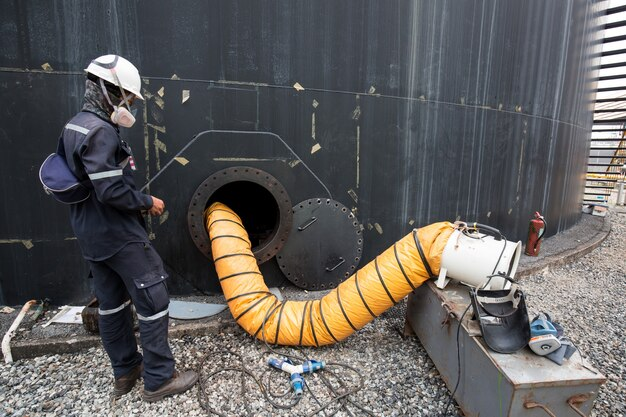
Isolating a Paint Spray Booth in a Manufacturing Plant
Background:
A manufacturing plant produces custom furniture, involving extensive use of spray painting. The existing spray booth was outdated and lacked adequate isolation, leading to:
- Air Pollution: Paint fumes and overspray escaping into the workspace, affecting worker health and product quality.
- Fire Hazard: Accumulated paint dust posing a significant fire risk.
- Inefficiency: Frequent cleaning disruptions due to overspray.
Solution:
The plant decided to isolate the spray booth by implementing the following measures:
- Dedicated Spray Booth Enclosure: A new, well-ventilated spray booth enclosure was constructed using non-combustible materials. The enclosure was equipped with:
- Negative Pressure System: To ensure air flows into the booth, preventing fumes from escaping.
- High-Efficiency Particulate Air (HEPA) Filters: To capture paint overspray and particulates.
- Explosion-Proof Lighting: To minimize fire hazards.
- Ventilation System: A dedicated ventilation system was installed to extract contaminated air from the booth and filter it before releasing it back into the atmosphere.
- Containment Measures:
- Spill Kits: Placed strategically within the booth to quickly contain any paint spills.
- Regular Cleaning: A strict cleaning schedule was implemented to prevent dust accumulation.
- Remote Operation: The spray guns were equipped with extended hoses, allowing workers to operate them from outside the booth, reducing exposure to fumes.
Results:
- Improved Air Quality: Significantly reduced paint fumes and overspray in the workspace, improving worker safety and comfort.
- Enhanced Product Quality: Minimized dust contamination on finished products.
- Increased Efficiency: Reduced cleaning time and disruptions.
- Reduced Fire Risk: Eliminated the risk of paint dust explosions.
Lessons Learned:
- Proper Planning: Thorough assessment of the existing situation and careful planning are crucial for successful isolation.
- Regulatory Compliance: Adhering to environmental regulations and safety standards is essential.
- Regular Maintenance: Consistent maintenance of the isolation system is necessary to ensure its effectiveness.
- Employee Training: Training employees on safe operating procedures and emergency response protocols is vital.
This case study demonstrates the effectiveness of isolating polluting equipment to improve safety, efficiency, and environmental performance. By implementing appropriate isolation measures, manufacturing facilities can create a safer and more sustainable working environment.
Note: This is a fictional case study for illustrative purposes. Actual situations and solutions may vary depending on specific circumstances and regulatory requirements.
White paper on Isolation of Polluting Equipment & Systems
A Critical Review
1. Introduction
Industrialization has brought about significant advancements, but it has also come at a cost to the environment. The release of pollutants from industrial processes poses a serious threat to human health, ecosystems, and the planet. This white paper explores the critical importance of isolating polluting equipment and systems, examining its benefits, challenges, and best practices.
2. The Need for Isolation
- Environmental Protection:
- Minimizes the release of harmful substances into the air, water, and soil.
- Protects biodiversity and natural resources.
- Mitigates climate change by reducing greenhouse gas emissions.
- Human Health:
- Reduces exposure to toxic substances, improving worker safety and public health.
- Prevents respiratory illnesses, cancers, and other health problems.
- Regulatory Compliance:
- Ensures adherence to environmental regulations and permits.
- Avoids costly fines and legal penalties.
- Economic Benefits:
- Reduces waste and improves resource efficiency.
- Protects brand reputation and enhances corporate social responsibility.
3. Isolation Methods
- Physical Barriers:
- Enclosures, chambers, and barriers to contain emissions.
- Examples: soundproof booths, fume hoods, containment vessels.
- Ventilation Systems:
- Capture and remove pollutants through specialized ventilation systems.
- Examples: scrubbers, filters, and local exhaust ventilation.
- Containment:
- Prevent the spread of pollutants through the use of containment mats, spill kits, and secondary containment structures.
- Remote Operation:
- Control polluting equipment from a distance to minimize human exposure.
- Process Modification:
- Alter production processes to reduce or eliminate pollution at the source.
4. Implementation Considerations
- Risk Assessment:
- Identify potential hazards and assess the risks associated with polluting equipment.
- Regulatory Compliance:
- Ensure compliance with all applicable environmental regulations and industry standards.
- Cost-Benefit Analysis:
- Evaluate the costs and benefits of different isolation methods.
- Maintenance and Monitoring:
- Implement regular maintenance and monitoring programs to ensure the effectiveness of isolation measures.
- Employee Training:
- Train employees on safe operating procedures and emergency response protocols.
5. Case Studies
- Manufacturing Plant: Isolation of a paint spray booth using a dedicated enclosure, ventilation system, and remote operation.
- Chemical Processing Facility: Implementation of a secondary containment system for hazardous waste storage tanks.
- Power Plant: Installation of scrubbers to reduce emissions from coal-fired power plants.
6. Conclusion
The isolation of polluting equipment and systems is crucial for environmental protection, human health, and regulatory compliance. By implementing effective isolation measures, industries can minimize their environmental impact, improve worker safety, and enhance their overall sustainability. Continued research and development in pollution control technologies are essential to address the evolving challenges of environmental pollution.
7. Recommendations
- Policymakers:
- Strengthen environmental regulations and incentives for pollution prevention.
- Promote the development and adoption of cleaner technologies.
- Industries:
- Invest in pollution control technologies and best practices.
- Prioritize environmental sustainability in their operations.
- Researchers:
- Develop innovative technologies for pollution control and monitoring.
By working together, policymakers, industries, and researchers can create a more sustainable future for all.
Disclaimer: This white paper provides general information and should not be considered legal or professional advice.
Note: This is a sample white paper and may require further research and customization to suit specific needs and applications.
Industrial Application of Isolation of Polluting Equipment & Systems
Courtesy: IndiaMART InterMESH Ltd
Isolation of polluting equipment and systems is a crucial practice across various industries to mitigate environmental impact, enhance worker safety, and ensure regulatory compliance. Here are some key industrial applications:
1. Manufacturing:
- Chemical Processing: Isolating reactors, distillation columns, and storage tanks for hazardous chemicals to prevent leaks and emissions.
- Paint Shops: Enclosing spray booths with negative pressure systems and high-efficiency particulate air (HEPA) filters to capture overspray and fumes.
- Metalworking: Isolating welding stations, grinding operations, and metal cutting processes to contain fumes, dust, and particulate matter.
- Pharmaceutical Manufacturing: Isolating sterile production areas to prevent contamination and ensure product quality.
2. Energy Production:
- Power Plants: Isolating coal-fired boilers and scrubbers to control emissions of sulfur dioxide, nitrogen oxides, and particulate matter.
- Oil and Gas Refineries: Isolating processing units and storage tanks to prevent leaks and spills of hydrocarbons and other pollutants.
3. Waste Management:
- Landfills: Isolating landfill cells with liners and leachate collection systems to prevent contamination of groundwater.
- Waste-to-Energy Plants: Isolating incineration chambers and flue gas treatment systems to control emissions of dioxins, furans, and other pollutants.
4. Research and Development:
- Laboratories: Isolating fume hoods, biosafety cabinets, and other equipment used to handle hazardous chemicals and biological materials.
5. Construction:
- Demolition Sites: Isolating demolition areas to control dust and debris emissions.
- Construction Sites: Isolating areas where hazardous materials like asbestos are being handled.
Benefits of Isolation in Industrial Settings:
- Improved Air Quality: Reduces exposure to harmful pollutants, improving worker health and safety.
- Enhanced Product Quality: Minimizes contamination of products due to airborne pollutants.
- Reduced Environmental Impact: Minimizes emissions to air, water, and soil, protecting ecosystems.
- Increased Efficiency: Reduces downtime for cleaning and maintenance.
- Regulatory Compliance: Ensures adherence to environmental regulations and permits.
- Improved Safety: Reduces the risk of accidents and incidents.
Key Considerations:
- Thorough Risk Assessment: Identify potential hazards and assess the risks associated with polluting equipment.
- Proper Design and Engineering: Ensure that isolation systems are properly designed, installed, and maintained.
- Regular Monitoring and Maintenance: Implement regular monitoring and maintenance programs to ensure the effectiveness of isolation measures.
- Employee Training: Train employees on safe operating procedures and emergency response protocols.
By implementing effective isolation strategies, industrial facilities can significantly reduce their environmental impact, improve worker safety, and enhance their overall sustainability.
Disclaimer: This information is for general knowledge and informational purposes only and does not constitute professional advice.
References
- ^ “Baghouse filter installation manifold – US Patent 5636422 Description”. Patentstorm.us. Archived from the original on 13 October 2012. Retrieved 6 August 2013.
- ^ “What is a Baghouse”. Baghouse.net. Archived from the original on 24 July 2013. Retrieved 6 August 2013.
- ^ “Baghouse / Fabric Filters KnowledgeBase”. Neundorfer.com. Archived from the original on 2013-08-07. Retrieved 6 August 2013.
- ^ Courtenay, John; Bryant, Michaek (July–August 2008). “Pleated cartridges provide increased baghouse capacity and improved filter performance” (PDF). Aluminium Times. Archived from the original (PDF) on 28 March 2012. Retrieved 6 August 2013.
- ^ “Cartridge Collectors”. Baghouse.com. 5 January 2011. Retrieved 6 August 2013.
- ^ Beachler, David S.; Joseph, Jerry; Pompelia, Mick (1995). “Fabric Filter Operation Overview” (PDF). North Carolina State University. Archived from the original (PDF) on 9 November 2013. Retrieved 6 August 2013.
- ^ Noyes, Robert (1991). Handbook of Pollution Control Processes. Noyes Publications. ISBN 9780815512905. Retrieved 6 August 2013.
- ^ Beachler, David S.; Joseph, Jerry; Pompelia, Mick (1995). “Lesson 2: Fabric Filter Bag Cleaning” (PDF). North Carolina State University. Archived from the original (PDF) on 9 November 2013. Retrieved 6 August 2013.
- ^ “About Us | Nederman”. www.nedermanmikropul.com. Retrieved 2021-07-21.
- ^ “Air filtration – Industrial Bag Filters and cartridges – Industrial Dedusting Filters”.
- ^ Jump up to:a b “Hunze LLC – Rotating Mechanical Cage”.
- ^ Beachler, David S.; Joseph, Jerry; Pompelia, Mick (1995). “Lesson 4:Fabric Filter Materials” (PDF). North Carolina State University. Retrieved 6 August 2013.[permanent dead link]
- ^ “Pleat+Plus Pleated Filter Bags”. Midwesco Filter Resources, Inc. Midwesco Filter Resources, Inc. Archived from the original on 2 June 2013. Retrieved 6 August 2013.