Building Operations and Maintenance- Building Operations and Maintenance (O&M) encompasses all the activities necessary to keep a building or facility functioning effectively and efficiently. It involves a wide range of tasks, from routine maintenance to major repairs and renovations.
Key Areas of Building O&M:
- Facilities Management: This involves overseeing the day-to-day operations of the building, including cleaning, security, and landscaping.Opens in a new windowfacilio.com Facilities Management in Building O&M
- HVAC Systems: Heating, ventilation, and air conditioning systems are critical for maintaining a comfortable and healthy indoor environment. O&M includes regular maintenance, repairs, and upgrades to these systems.Opens in a new windowpreventivemaintenanceprocedure.com HVAC Systems in Building O&M
- Plumbing Systems: Ensuring the proper functioning of plumbing systems, including water supply, drainage, and sewage disposal, is essential for building safety and hygiene. O&M involves regular inspections, repairs, and replacements as needed.Opens in a new windowdailycivil.com Plumbing Systems in Building O&M
- Electrical Systems: Maintaining the electrical systems, including wiring, lighting, and power distribution, is crucial for safety and operational efficiency. O&M includes regular inspections, repairs, and upgrades to ensure compliance with safety standards.Opens in a new windowmontajstructura.ro Electrical Systems in Building O&M
- Building Envelope: The exterior of the building, including the roof, walls, and windows, plays a vital role in protecting the building’s interior and occupants. O&M includes regular inspections, repairs, and maintenance to prevent leaks, drafts, and other issues.Opens in a new windowwww.buildings.com Building Envelope in Building O&M
- Fire Safety Systems: Ensuring the proper functioning of fire safety systems, including fire alarms, sprinklers, and extinguishers, is critical for occupant safety. O&M includes regular inspections, testing, and maintenance of these systems.Opens in a new windowwww.buildings.com Fire Safety Systems in Building O&M
- Energy Management: Implementing energy-efficient practices and technologies can significantly reduce operating costs and environmental impact. O&M includes monitoring energy consumption, identifying areas for improvement, and implementing energy-saving measures.Opens in a new windowwww.mdpi.com Energy Management in Building O&M
Benefits of Effective Building O&M:
- Increased Building Lifespan: Regular maintenance and proactive repairs can extend the lifespan of building components and systems.
- Improved Energy Efficiency: Implementing energy-saving measures can reduce operating costs and environmental impact.
- Enhanced Occupant Comfort: Well-maintained buildings provide a more comfortable and productive environment for occupants.
- Reduced Risk of Emergencies: Regular inspections and maintenance can help prevent costly emergencies, such as fires or floods.
- Increased Property Value: A well-maintained building is more attractive to tenants and buyers, which can increase its value.
By implementing effective Building O&M practices, building owners and managers can ensure the safety, comfort, and efficiency of their facilities while also protecting their investment.
What is Required Building Operations and Maintenance
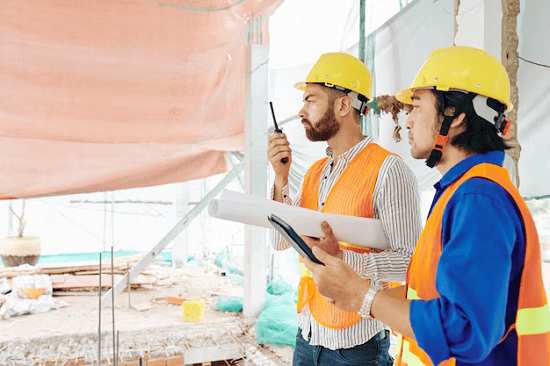
Required Building Operations and Maintenance can vary depending on the specific building type, local regulations, and industry standards. However, some essential tasks and considerations include:
Safety and Compliance:
- Fire Safety Systems: Regular inspections, testing, and maintenance of fire alarms, sprinklers, and extinguishers are crucial for occupant safety.
- Emergency Exits: Ensuring all emergency exits are clearly marked, unobstructed, and properly maintained.
- Electrical Systems: Regular inspections and maintenance of electrical systems, including wiring, lighting, and power distribution, to ensure safety and compliance with electrical codes.
- Accessibility: Ensuring compliance with accessibility standards for people with disabilities, including ramps, elevators, and restrooms.
Essential Building Systems:
- HVAC Systems: Regular maintenance, filter replacements, and repairs to ensure optimal heating, ventilation, and air conditioning performance.
- Plumbing Systems: Regular inspections and repairs to prevent leaks, clogs, and other plumbing issues.
- Elevators: Regular maintenance and safety inspections by certified technicians.
- Building Envelope: Regular inspections and maintenance of the building’s exterior, including the roof, walls, and windows, to prevent leaks, drafts, and water damage.
General Maintenance:
- Cleaning and Sanitation: Regular cleaning of common areas, restrooms, and other spaces to maintain a hygienic environment.
- Pest Control: Regular pest control measures to prevent infestations and protect building occupants.
- Landscaping: Maintaining the exterior grounds, including mowing lawns, trimming shrubs, and removing debris.
- Security: Implementing security measures, such as surveillance systems, access control, and security personnel, to protect the building and its occupants.
Additional Considerations:
- Energy Management: Implementing energy-efficient practices and technologies to reduce operating costs and environmental impact.
- Waste Management: Implementing waste management programs, including recycling and composting, to reduce waste and promote sustainability.
- Building Codes and Regulations: Ensuring compliance with all applicable building codes and regulations, including fire codes, electrical codes, and accessibility standards.
Documentation and Record-Keeping:
- Maintaining accurate records of all maintenance activities, inspections, and repairs.
- Creating and maintaining a preventative maintenance schedule to ensure timely and proactive maintenance.
By adhering to these requirements, building owners and managers can ensure the safety, functionality, and longevity of their properties while also providing a comfortable and productive environment for occupants.
Who is Required Building Operations and Maintenance
Courtesy: AASHE
Building Operations and Maintenance (O&M) is typically the responsibility of the building owner or property manager.
- Building Owners: Ultimately responsible for ensuring the building is safe, functional, and compliant with all regulations.
- Property Managers: Often hired by building owners to oversee day-to-day operations, manage maintenance tasks, and coordinate with contractors.
In some cases, occupants may have specific responsibilities, such as:
- Tenants: May be responsible for maintaining their own units, such as cleaning and minor repairs.
- Homeowners: In residential settings, homeowners are generally responsible for maintaining their own properties.
Specialized Contractors: May be hired for specific tasks, such as:
- HVAC maintenance
- Electrical repairs
- Plumbing services
- Pest control
- Landscaping
The specific responsibilities for Building O&M will depend on the type of building, local regulations, and the terms of any lease agreements.
When is Required Building Operations and Maintenance
Required Building Operations and Maintenance should be conducted on an ongoing basis.
- Preventive Maintenance: This involves regular inspections, cleaning, and minor repairs to prevent major problems from occurring. The frequency of preventive maintenance will vary depending on the specific system or component.
- Corrective Maintenance: This involves repairing or replacing equipment or systems that have failed or are malfunctioning. Corrective maintenance should be performed as soon as possible to minimize disruption and prevent further damage.
In addition to ongoing maintenance, some tasks may be required on a specific schedule:
- Annual Inspections: Many building systems, such as fire safety systems and elevators, require annual inspections by qualified professionals.
- Seasonal Maintenance: Some tasks, such as checking and cleaning HVAC systems, may be performed more frequently during certain seasons.
- As-Needed Maintenance: Repairs and replacements may be required as needed, such as after a storm or other unforeseen event.
By implementing a comprehensive Building O&M program that includes both preventive and corrective maintenance, building owners and managers can ensure the safety, functionality, and longevity of their properties.
Where is Required Building Operations and Maintenance
Building Operations and Maintenance (O&M) is required throughout the entire building.
Here’s a breakdown:
- Interior Spaces:
- Common Areas: Lobbies, hallways, restrooms, elevators, and other shared spaces require regular cleaning, maintenance, and repairs.
- Tenant Spaces: While tenants may be responsible for maintaining their own units, building owners are responsible for the structural integrity and major systems within those spaces.
- Exterior Spaces:
- Building Envelope: The roof, walls, windows, and doors require regular inspections and maintenance to prevent leaks, drafts, and water damage.
- Landscaping: Maintaining the grounds, including mowing lawns, trimming shrubs, and removing debris, is essential for the building’s appearance and safety.
- Parking Lots and Driveways: Regular inspections and repairs to ensure safety and accessibility.
Essentially, any part of the building that contributes to its functionality, safety, and appearance requires ongoing O&M.
How is Required Building Operations and Maintenance
Courtesy: Electrical Engineering Topics
Building Operations and Maintenance (O&M) is typically carried out through a combination of methods:
- Preventive Maintenance: This proactive approach involves regular inspections, cleaning, and minor repairs to prevent major problems from occurring.
- Regular Inspections: Visual inspections of building systems and components to identify potential issues early on.
- Routine Cleaning: Regular cleaning of common areas, restrooms, and other spaces to maintain a hygienic and presentable environment.
- Minor Repairs: Promptly addressing minor issues, such as fixing leaks, replacing light bulbs, and repairing minor damage.
- Scheduled Maintenance: Performing routine maintenance tasks on a predetermined schedule, such as changing HVAC filters, lubricating moving parts, and testing emergency systems.
- Corrective Maintenance: This reactive approach involves repairing or replacing equipment or systems that have failed or are malfunctioning.
- Emergency Repairs: Addressing urgent issues that require immediate attention, such as power outages, plumbing leaks, or fire alarms.
- Major Repairs: Undertaking more significant repair projects, such as replacing HVAC units, repairing structural damage, or renovating specific areas of the building.
- Technology-Enabled Solutions: Utilizing technology to improve O&M efficiency and effectiveness.
- Building Management Systems (BMS): Monitoring and controlling building systems, such as HVAC, lighting, and security, through a centralized system.
- Computerized Maintenance Management Systems (CMMS): Software programs that help track maintenance activities, schedule tasks, and manage inventory.
- IoT Sensors: Using sensors to monitor building conditions, such as temperature, humidity, and energy consumption, to identify potential problems and optimize operations.
By combining these methods, building owners and managers can implement a comprehensive O&M program that ensures the safety, functionality, and longevity of their properties.
Case Study on Building Operations and Maintenance
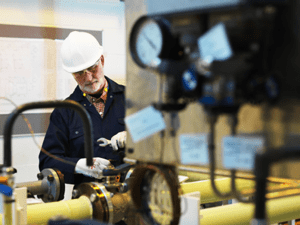
Enhancing Building Operations and Maintenance in a Large Office Complex
Background:
A large office complex in a bustling metropolitan area was experiencing escalating operational costs, frequent equipment failures, and declining tenant satisfaction. The building management team recognized the need for a comprehensive overhaul of their Building Operations and Maintenance (O&M) strategy.
Challenges:
- Reactive Maintenance: The existing approach was primarily reactive, leading to costly emergency repairs and unplanned downtime.
- Inefficient Resource Allocation: Lack of a centralized system resulted in inefficient scheduling, poor communication, and underutilized resources.
- High Energy Consumption: Outdated equipment and inefficient practices contributed to high energy consumption and environmental impact.
- Declining Tenant Satisfaction: Frequent disruptions and uncomfortable working conditions led to tenant dissatisfaction and potential revenue loss.
Solution:
The building management team implemented a multi-pronged approach to address these challenges:
- Implementing a Computerized Maintenance Management System (CMMS):
- A CMMS was implemented to track maintenance activities, schedule preventive maintenance tasks, manage inventory, and generate reports.
- This centralized system improved communication between maintenance staff, contractors, and tenants.
- It also facilitated data-driven decision-making by providing insights into equipment performance, maintenance costs, and energy consumption.
- Energy Efficiency Upgrades:
- A comprehensive energy audit was conducted to identify areas for improvement.
- Upgrades were made to HVAC systems, lighting fixtures, and building automation controls to reduce energy consumption.
- This not only reduced operational costs but also improved tenant comfort and environmental sustainability.
- Preventive Maintenance Program:
- A robust preventive maintenance program was established to identify and address potential issues before they escalated into major problems.
- Regular inspections, cleaning, and minor repairs were scheduled for all building systems and components.
- This proactive approach significantly reduced the frequency and severity of equipment failures, minimizing disruptions and associated costs.
- Tenant Engagement:
- Regular communication with tenants was established to address their concerns and gather feedback.
- Tenant satisfaction surveys were conducted to identify areas for improvement in building operations and maintenance.
- This feedback was used to refine the O&M strategy and enhance the overall tenant experience.
Results:
- Reduced Operational Costs: The implementation of a CMMS, energy efficiency upgrades, and a preventive maintenance program resulted in a significant reduction in operational costs.
- Improved Equipment Reliability: The proactive maintenance approach minimized equipment failures, reducing downtime and associated costs.
- Enhanced Tenant Satisfaction: Improved building conditions, reduced disruptions, and responsive maintenance practices led to increased tenant satisfaction and retention.
- Increased Sustainability: Energy efficiency upgrades and sustainable practices reduced the building’s environmental impact.
Conclusion:
By adopting a proactive and data-driven approach to Building Operations and Maintenance, the building management team was able to achieve significant improvements in efficiency, cost-effectiveness, and tenant satisfaction. This case study demonstrates the importance of a well-planned and executed O&M strategy for the long-term success of any building.
Note: This is a fictionalized case study for illustrative purposes. Actual results may vary depending on the specific circumstances and challenges faced by each building.
White paper on Building Operations and Maintenance
Optimizing Building Operations and Maintenance for Enhanced Performance and Sustainability
Abstract:
This white paper explores the critical role of effective Building Operations and Maintenance (O&M) in ensuring the safety, functionality, and longevity of buildings. It delves into key O&M strategies, including preventive maintenance, corrective maintenance, and technology-enabled solutions. Furthermore, the paper emphasizes the significance of sustainability considerations within O&M practices, highlighting the benefits of energy efficiency, waste reduction, and environmental stewardship.
1. Introduction:
Building Operations and Maintenance (O&M) encompasses all activities necessary to keep a building or facility functioning effectively and efficiently. It involves a wide range of tasks, from routine maintenance to major repairs and renovations. Effective O&M is crucial for:
- Ensuring occupant safety and comfort: Maintaining essential building systems, such as fire safety, HVAC, and plumbing, is paramount for occupant safety and well-being.
- Extending building lifespan: Regular maintenance and proactive repairs can significantly extend the lifespan of building components and systems.
- Reducing operational costs: Implementing energy-efficient practices and technologies can significantly reduce operating costs and environmental impact.
- Increasing property value: Well-maintained buildings are more attractive to tenants and buyers, which can increase their value.
2. Key O&M Strategies:
- Preventive Maintenance: This proactive approach involves regular inspections, cleaning, and minor repairs to prevent major problems from occurring.
- Benefits: Reduced equipment failures, minimized downtime, and extended equipment lifespan.
- Examples: Regular HVAC filter replacements, lubrication of moving parts, and visual inspections of building systems.
- Corrective Maintenance: This reactive approach involves repairing or replacing equipment or systems that have failed or are malfunctioning.
- Importance: Addressing urgent issues promptly to minimize disruption and prevent further damage.
- Examples: Emergency repairs for plumbing leaks, power outages, and fire alarms.
- Technology-Enabled Solutions: Utilizing technology to improve O&M efficiency and effectiveness.
- Building Management Systems (BMS): Monitoring and controlling building systems, such as HVAC, lighting, and security, through a centralized system.
- Computerized Maintenance Management Systems (CMMS): Software programs that help track maintenance activities, schedule tasks, and manage inventory.
- Internet of Things (IoT) Sensors: Using sensors to monitor building conditions, such as temperature, humidity, and energy consumption, to identify potential problems and optimize operations.
3. Sustainability in Building O&M:
- Energy Efficiency: Implementing energy-efficient practices and technologies, such as upgrading lighting fixtures, optimizing HVAC systems, and utilizing renewable energy sources.
- Waste Reduction: Implementing waste management programs, including recycling and composting, to minimize waste and promote sustainability.
- Water Conservation: Implementing water-saving measures, such as low-flow fixtures and rainwater harvesting systems, to reduce water consumption.
- Indoor Environmental Quality (IEQ): Ensuring good indoor air quality by implementing proper ventilation, filtration, and control of pollutants.
4. Challenges and Considerations:
- Budget Constraints: Balancing the need for O&M with budget limitations can be challenging.
- Staffing and Training: Ensuring adequate staffing and training for O&M personnel is crucial for effective implementation.
- Compliance with Regulations: Adhering to building codes, safety regulations, and environmental standards.
- Technological Integration: Integrating various technologies and systems can be complex and require specialized expertise.
5. Conclusion:
Effective Building Operations and Maintenance is essential for ensuring the safety, functionality, and sustainability of buildings. By implementing a comprehensive O&M strategy that incorporates preventive maintenance, corrective maintenance, and technology-enabled solutions, building owners and managers can optimize building performance, reduce operational costs, and enhance the overall occupant experience. Furthermore, integrating sustainability considerations into O&M practices is crucial for creating environmentally responsible and resilient buildings.
6. Recommendations:
- Conduct regular building assessments to identify areas for improvement.
- Develop a comprehensive O&M plan that includes preventive maintenance schedules, emergency procedures, and resource allocation strategies.
- Invest in energy-efficient technologies and sustainable practices.
- Continuously monitor and evaluate O&M performance to identify areas for improvement.
- Foster a culture of safety and sustainability among building occupants.
Note: This white paper provides a general overview of Building Operations and Maintenance. Specific O&M requirements and strategies will vary depending on the type of building, local regulations, and individual needs.
Disclaimer: This white paper is for informational purposes only and does not constitute professional advice.
Industrial Application of Building Operations and Maintenance
Courtesy: FacilitiesNet
In industrial settings, Building Operations and Maintenance (O&M) takes on critical importance, directly impacting production, safety, and profitability. Here’s a breakdown of key industrial applications:
1. Production Continuity:
- Minimizing Downtime: Industrial facilities rely heavily on uninterrupted operations. Effective O&M minimizes unplanned downtime caused by equipment failures, power outages, or environmental issues.
- Maintaining Production Efficiency: Well-maintained equipment and infrastructure ensure optimal production flow and output.
- Preventing Catastrophic Failures: Proactive maintenance can prevent major equipment breakdowns that can halt production for extended periods, leading to significant financial losses.
2. Safety and Compliance:
- Ensuring Worker Safety: Industrial environments often involve hazardous materials and heavy machinery. O&M plays a crucial role in ensuring a safe working environment by maintaining safety systems, addressing potential hazards, and complying with industry regulations.
- Environmental Compliance: Industrial facilities must adhere to environmental regulations. O&M practices contribute to environmental compliance by minimizing pollution, conserving energy, and managing waste effectively.
- Fire and Safety Systems: Regular inspection and maintenance of fire suppression systems, emergency exits, and safety equipment are critical for worker safety and compliance with fire codes.
3. Energy Efficiency and Cost Reduction:
- Optimizing Energy Consumption: Industrial facilities often have high energy demands. O&M practices can significantly reduce energy consumption through measures like:
- Implementing energy-efficient lighting systems
- Optimizing HVAC systems
- Utilizing energy-efficient equipment
- Reducing Operating Costs: By minimizing downtime, preventing costly repairs, and optimizing energy consumption, O&M contributes to significant cost savings.
- Waste Reduction: Implementing waste management programs, including recycling and waste reduction initiatives, can reduce environmental impact and operating costs.
4. Technology Integration:
- Industrial IoT (IIoT): Integrating IIoT sensors and technologies into O&M practices enables:
- Predictive maintenance
- Real-time monitoring of equipment health
- Remote diagnostics
- Improved energy management
- Building Management Systems (BMS): Centralized control and monitoring of building systems, such as HVAC, lighting, and security, enhance efficiency and energy savings.
5. Specific Industrial Applications:
- Manufacturing: Maintaining production lines, ensuring proper ventilation, and managing hazardous waste.
- Warehousing: Ensuring proper storage conditions, maintaining material handling equipment, and managing inventory.
- Data Centers: Maintaining critical infrastructure, ensuring uninterrupted power supply, and managing cooling systems.
Key Considerations for Industrial O&M:
- Risk Assessment: Conducting thorough risk assessments to identify potential hazards and prioritize maintenance activities.
- Specialized Expertise: Employing skilled maintenance personnel with expertise in industrial equipment and systems.
- Compliance with Industry Standards: Adhering to industry-specific regulations and best practices.
- Continuous Improvement: Regularly reviewing and refining O&M practices to enhance efficiency and effectiveness.
By effectively implementing Building Operations and Maintenance strategies, industrial facilities can optimize production, enhance safety, reduce costs, and achieve long-term sustainability.
References
- The Institute of Residential Property Management
- The Association of Residential Managing Agents
- Facilities Management Association
- Japanese apartment management
- British Institute of Facilities Management
- Park, A. (1994) Facilities Management: An Explanation. Palgrave NY.
- “Defense Logistics Agency”. DLA.mil. Retrieved 5 August 2016.
- ^ “European Federation of National Maintenance Societies”. EFNMS.org. Retrieved 5 August 2016.
All actions which have the objective of retaining or restoring an item in or to a state in which it can perform its required function. These include the combination of all technical and corresponding administrative, managerial, and supervision actions.
- ^ Jump up to:a b Ken Staller. “Defining Preventive & Predictive Maintenance”.
- ^ “MRO – Definition”. RF System Lab.
- ^ Jump up to:a b c d e Federal Standard 1037C and from MIL-STD-188 and from the Department of Defense Dictionary of Military and Associated Terms
- ^ “AAP-6 – Glossary of terms and definitions”. NATO Standardization Agency. North Atlantic Treaty Organization: 158.
- ^ United States Code of Federal Regulations Title 14, Part 43 – Maintenance, Preventive Maintenance, Rebuilding, and Alteration
- ^ Airworthiness Manual, Doc 9760 (3 ed.). Montreal (Canada): International Civil Aviation Organization. 2014. p. 375. ISBN 978-92-9249-454-4. Archived from the original on 2018-09-01. Retrieved 2018-02-18.
The Airworthiness Manual (Doc 9760) contains a consolidation of airworthiness-related information previously found in other ICAO documents … provides guidance to States on how to meet their airworthiness responsibilities under the Convention on International Civil Aviation. This third edition is presented based on States’ roles and responsibilities, thus as State of Registry, State of the Operator, State of Design and State of Manufacture. It also describes the interface between different States and their related responsibilities. It has been updated to incorporate changes to Annex 8 to the Chicago Convention — Airworthiness of Aircraft, and to Annex 6 — Operation of Aircraft
- ^ Berendsen, A. M.; Springer (2013). Marine Painting Manual (1st ed.). ISBN 978-90-481-8244-2.
- ^ Jump up to:a b ISO 12944-9:2018 – Paints and Varnishes – Corrosion Protection of Steel Structures by Protective Paint Systems – Part 9: Protective Paint Systems and Laboratory Performance Test Methods for Offshore and Related Structures.
- ^ Singhvi, Anjali; Gröndahl, Mika (January 1, 2019). “What’s Different in the M.T.A.’s New Plan for Repairing the L Train Tunnel”. The New York Times.
- ^ Charles Velson Horie (2010). Materials for Conservation: Organic Consolidants, Adhesives and Coatings (2nd ed.). Butterworth-Heinemann. ISBN 978-0-75-066905-4.
- ^ Jump up to:a b Micharl Decourcy Hinds (February 17, 1985). “Preventive Maintenance: A Checklist”. The New York Times.
- ^ Erik Sandberg-Diment (August 14, 1984). “Personal computers preventive maintenance for an aging computer”. The New York Times.
- ^ “6 Tips to Keep Your Machine Cool in Summer | Al Marwan”. Al Marwan Heavy Machinery. Retrieved 2024-06-20.
- ^ Ben Zimmer (April 18, 2010). “Wellness”. The New York Times.
Complaints about preventative go back to the late 18th century … (“Oxford English Dictionary dates preventive to 1626 and preventative to 1655) ..preventive has won”
- ^ O. A. Bamiro; D. Nzediegwu; K. A. Oladejo; A. Rahaman; A. Adebayo (2011). Mastery of Technology for Junior School Certificate Examination. Ibadan: Evans Brothers (Nigeria Publishers) Limited.
- ^ Jump up to:a b “CPOL: System Maintenance and Downtime Announcements”. Retrieved March 21, 2019.
… out of service from 6:00–7:00am Eastern for regularly scheduled maintenance.
- ^ Jump up to:a b “Dodge City Radar Planned Maintenance”. weather.gov (National Weather Service).
… will be down for approximately five days
- ^ Jump up to:a b “The development of a cost benefit analysis method for monitoring the condition of batch” (PDF). Archived (PDF) from the original on March 22, 2019.
- ^ “What is PPM Maintenance?”.
- ^ e.g. from leaks that could have been prevented
- ^ Wood, Brian (2003). Building care. Wiley-Blackwell. ISBN 978-0-632-06049-8. Retrieved 2011-04-22.
- ^ Garcia, Mari Cruz; Sanz-Bobi, Miguel A.; Del Pico, Javier (August 2006), “SIMAP: Intelligent System for Predictive Maintenance: Application to the health condition monitoring of a windturbine gearbox”, Computers in Industry, 57 (6): 552–568, doi:10.1016/j.compind.2006.02.011
- ^ Kaiser, Kevin A.; Gebraeel, Nagi Z. (12 May 2009), “Predictive Maintenance Management Using Sensor-Based Degradation Models”, IEEE Transactions on Systems, Man, and Cybernetics – Part A: Systems and Humans, 39 (4): 840–849, doi:10.1109/TSMCA.2009.2016429, hdl:1853/56106, S2CID 5975976
- ^ “Spacewalking Astronauts Swap Out Space Station’s Batteries”. The New York Times. March 22, 2019. Retrieved March 22, 2019.
- ^ such as universities and local schools, which write government-acceptable receipts
- ^ CBM Policy Memorandum.
- ^ Liu, Jie; Wang, Golnaraghi (2010). “An enhanced diagnostic scheme for bearing condition monitoring”. IEEE Transactions on Instrumentation and Measurement. 59 (2): 309–321. Bibcode:2010ITIM…59..309L. doi:10.1109/tim.2009.2023814. S2CID 1892843.
- ^ Jardine, A.K.S.; Lin, Banjevic (2006). “A review on machinery diagnostics and prognostics implementing condition-based maintenance”. Mechanical Systems and Signal Processing. 20 (7): 1483–1510. Bibcode:2006MSSP…20.1483J. doi:10.1016/j.ymssp.2005.09.012.
- ^ Industrial Polymer Applications: Essential Chemistry and Technology (1st ed.). United Kingdom: Royal Society of Chemistry. 2016. ISBN 978-1782628149.