Minimum Energy Performance- “Minimum Energy Performance” (MEP) generally refers to the lowest level of energy efficiency or performance that buildings, systems, or appliances are required to meet by regulations or standards. These requirements are often set by governments, organizations, or industry bodies to ensure that energy use is optimized, reducing waste and improving sustainability. MEP standards are often applied to:
- Buildings: In construction, MEP standards may cover insulation, heating, ventilation, and air conditioning (HVAC) systems, lighting, and other aspects that contribute to the energy performance of a building.
- Appliances: For products like refrigerators, air conditioners, and water heaters, there are MEP standards that define the minimum energy efficiency levels these appliances must meet in order to be sold or used.
- Energy Codes and Regulations: These are legal requirements that enforce minimum energy performance for building designs or retrofits, often part of national or local building codes.
- Energy Star Ratings: In some contexts, minimum energy performance is linked to energy labeling systems, such as Energy Star, which certifies that a product meets certain energy performance criteria.
The goal of MEP requirements is to reduce overall energy consumption, lower operating costs, and minimize environmental impact through improved energy efficiency.
What is Required Minimum Energy Performance
The Required Minimum Energy Performance (RMEP) refers to the lowest energy performance level that must be met in certain buildings, systems, or appliances as set by regulations, building codes, or industry standards. These requirements are designed to ensure that the energy consumption of a building or product is optimized and that energy is not wasted, contributing to both cost savings and sustainability goals.
RMEP is typically defined by:
1. Building Codes
- Many countries and regions have building energy codes that specify minimum energy performance for new buildings or significant renovations. This can include limits on:
- Insulation levels (to prevent heat loss or gain)
- Energy-efficient windows and doors
- Heating, ventilation, and air-conditioning (HVAC) systems that meet energy efficiency standards
- Lighting and electrical systems that reduce energy use
- For example, in the U.S., codes like the International Energy Conservation Code (IECC) set minimum energy standards for residential and commercial buildings.
2. Appliance and Product Standards
- Many appliances (like refrigerators, washing machines, air conditioners, etc.) must meet minimum energy performance standards set by regulatory bodies like the U.S. Department of Energy (DOE) or European Union regulations. These standards ensure that products:
- Use energy efficiently
- Do not exceed specified energy consumption limits for their category
- For instance, appliances may need to meet or exceed certain Energy Star ratings or other national standards to be sold legally.
3. Energy Performance Certificates
- In some regions, buildings must obtain an Energy Performance Certificate (EPC) that shows how energy efficient the building is. These certificates indicate whether a building meets or exceeds the required minimum energy performance standards.
4. Renovation and Retrofitting
- Minimum energy performance standards are also applied to renovations and retrofits. For example, when a building undergoes significant renovations, it may need to meet current energy performance standards for insulation, HVAC systems, and electrical systems.
5. Compliance with International Standards
- There are international energy performance frameworks, such as the International Organization for Standardization (ISO) standards on energy efficiency, which might define required minimum energy performance for specific types of buildings, products, or industries.
Purpose and Goals:
The goal of these requirements is to:
- Reduce energy consumption and carbon emissions, helping to meet environmental sustainability targets.
- Lower operating costs for building owners and residents.
- Ensure that energy use is optimized for economic and environmental benefit.
Examples of RMEP:
- Residential Buildings: A new home may need to meet the RMEP for insulation, HVAC efficiency, and window performance as dictated by local building codes (e.g., in the U.S., meeting the standards in the IECC).
- Commercial Buildings: Larger buildings may need to comply with more stringent energy performance regulations (e.g., Deming Rating certification, ASHRAE standards).
- Appliances: A refrigerator might have to meet a certain energy efficiency standard, such as the DOE’s minimum allowable energy consumption rate for refrigerators.
Who is Required Minimum Energy Performance
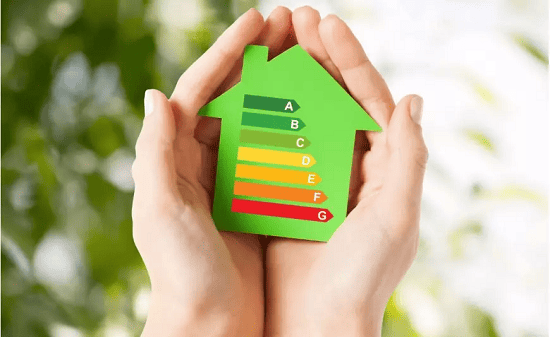
The Required Minimum Energy Performance (RMEP) standards apply to various stakeholders, including individuals, organizations, and industries involved in the construction, renovation, purchase, or use of buildings and products. Here’s a breakdown of who is required to meet these standards:
1. Building Owners and Developers
- New Construction: Anyone constructing new buildings, whether residential, commercial, or industrial, is required to comply with minimum energy performance standards. These standards are typically enforced through building codes and energy efficiency regulations that mandate certain levels of insulation, HVAC systems, lighting, and other building features.
- Renovations and Retrofits: Property owners undertaking renovations or retrofitting projects must ensure that the building meets current energy performance standards. This is particularly true for major upgrades like installing new heating systems, windows, or insulation.
2. Architects, Engineers, and Designers
- Professionals involved in the design and planning of buildings or systems are responsible for ensuring that their designs meet minimum energy performance standards. This includes integrating energy-efficient systems, optimizing insulation, designing for natural light, and incorporating renewable energy sources where feasible.
- They must be familiar with local, regional, or national energy codes and regulations (e.g., International Energy Conservation Code (IECC), ASHRAE standards, etc.).
3. Contractors and Builders
- Builders and contractors must follow the prescribed construction methods, materials, and systems that meet or exceed energy performance standards. They are responsible for ensuring that installations, such as windows, insulation, and HVAC systems, are energy efficient and comply with the required codes.
4. Manufacturers and Suppliers
- Appliance Manufacturers: Companies that manufacture appliances like refrigerators, air conditioners, water heaters, etc., must ensure their products meet minimum energy efficiency requirements set by regulatory bodies (e.g., U.S. Department of Energy (DOE) or European Union regulations). These products may be required to have energy labels like Energy Star or meet specific energy consumption limits.
- Material Suppliers: Suppliers of building materials, such as insulation, windows, and lighting systems, must provide products that meet the energy performance standards required by the construction codes.
5. Property Managers and Facility Operators
- Property managers and those responsible for maintaining buildings must ensure that the buildings operate efficiently and continue to meet energy performance standards. This may include regular maintenance of heating and cooling systems, lighting controls, and insulation, as well as the implementation of energy-saving practices.
6. Government and Regulatory Bodies
- Regulatory Authorities: Governments, local authorities, and regulatory bodies establish and enforce energy performance standards through laws, building codes, and regulations. These authorities monitor compliance and ensure that the required standards are met during construction, renovation, and product sales.
7. Consumers and Homeowners
- Homeowners: Homeowners must comply with RMEP standards when building or renovating their homes, particularly when making substantial changes like installing new HVAC systems or windows. They must also ensure that appliances they purchase meet minimum energy efficiency standards.
8. Businesses and Industries
- Commercial Building Owners: Companies that own or lease commercial properties must ensure that these buildings comply with energy efficiency regulations. In addition, they may need to adopt energy-saving technologies or practices to reduce consumption.
- Manufacturers and Industrial Plants: Factories and manufacturing facilities are required to meet minimum energy performance standards for their machinery, lighting, heating, and cooling systems to optimize energy use and reduce environmental impact.
Specific Examples:
- A Developer constructing a new office building must ensure that the building’s insulation, heating, cooling, and lighting systems meet energy performance codes.
- A Homeowner renovating their kitchen may need to install energy-efficient appliances, such as an Energy Star-rated refrigerator, to comply with local building codes.
- A Manufacturer producing air conditioning units is required to meet energy efficiency standards set by agencies like the DOE.
Conclusion:
Essentially, anyone involved in the creation, sale, or use of energy-consuming products or systems is required to meet RMEP standards. These regulations are in place to help reduce energy consumption, cut operating costs, and promote sustainability in various sectors, from construction and manufacturing to product sales and facility operations.
When is Required Minimum Energy Performance
The Required Minimum Energy Performance (RMEP) standards apply in various contexts, and the timing of when they need to be met can depend on the specific situation, location, and type of building or product involved. Here are key instances when RMEP must be adhered to:
1. During New Construction
- When: RMEP standards must be met at the time of construction or design for new buildings or structures.
- What: New buildings (residential, commercial, or industrial) must comply with minimum energy performance standards set by local or national building codes, such as the International Energy Conservation Code (IECC), or ASHRAE standards.
- Why: To ensure that energy-efficient features like insulation, windows, HVAC systems, and lighting are integrated into the building design, helping to reduce energy consumption from the start.
2. During Major Renovations or Retrofits
- When: RMEP standards apply when a building undergoes significant renovations, such as replacing HVAC systems, windows, or insulation, or when a major retrofit is planned.
- What: A building may be required to meet current energy performance standards during the renovation. This includes updating heating and cooling systems, improving insulation, and possibly adding renewable energy sources.
- Why: Renovations offer the opportunity to improve a building’s energy performance, ensuring it aligns with modern efficiency standards and reducing future energy consumption.
3. During Property or Building Purchases
- When: When a property is bought, RMEP standards may apply to the renovation or updating of systems and appliances in the building to meet current energy standards.
- What: This might require the owner to upgrade or replace appliances, lighting, or HVAC systems if they do not meet required energy performance levels.
- Why: Energy efficiency laws ensure that properties meet baseline energy standards after changes in ownership or occupancy.
4. When Purchasing Appliances or Products
- When: At the time of purchase of certain appliances, equipment, or consumer products.
- What: Products like refrigerators, washing machines, air conditioners, and other energy-consuming appliances must meet minimum energy performance standards (e.g., Energy Star certification) at the time of sale.
- Why: To ensure that these products are energy-efficient and meet the environmental and economic goals set by regulatory bodies.
5. When a Building or Product is Installed or Modified
- When: During the installation or major modification of energy systems (e.g., HVAC systems, lighting systems, insulation).
- What: If a system or product is being installed for the first time, or if an existing system is being modified (e.g., replacing an outdated furnace with a newer, more efficient one), it must meet the applicable RMEP standards.
- Why: To minimize energy waste and ensure the building or system operates efficiently over its lifetime.
6. For Ongoing Compliance (for Existing Buildings)
- When: In some cases, compliance is required periodically for ongoing operations or when buildings undergo energy audits.
- What: Existing buildings may need to undergo energy audits to confirm they still meet the required energy performance levels or undergo retrofits to bring them up to standard.
- Why: As part of energy efficiency programs, periodic assessments can help ensure that energy performance remains high and operational costs are kept low.
7. When Enforced by Local or National Regulations
- When: RMEP standards must be met when required by local building codes, national regulations, or specific industry standards.
- What: These regulations may have deadlines or compliance dates that trigger the need to meet RMEP standards.
- Why: Governments and regulatory bodies set these requirements to ensure that energy use is minimized and that buildings and products contribute to sustainability efforts.
Key Examples of Timing:
- New Residential Building: A new home being built must meet the RMEP standards at the time of construction (e.g., insulation levels, efficient HVAC systems, and windows).
- Renovation of an Office Building: If a commercial property undergoes major renovations (e.g., replacing windows or upgrading the heating system), it must meet current energy efficiency standards at the time of renovation.
- Appliance Purchase: When purchasing a new air conditioning unit, it must meet minimum energy performance standards at the time of sale, ensuring it is energy-efficient and compliant with regulations.
Conclusion:
The timing for meeting Required Minimum Energy Performance standards depends on the project, product, or system being dealt with. The key points are that RMEP applies at the time of construction, renovation, installation, purchase, or when compliance with building codes is required. These regulations ensure that energy consumption is optimized from the outset, reducing waste and lowering costs in the long term.
Where is Required Minimum Energy Performance
The Required Minimum Energy Performance (RMEP) standards are enforced globally but vary by location, depending on national, regional, or local regulations. These standards are typically applied to buildings, appliances, and industrial equipment to ensure they meet specific energy efficiency requirements.
Here are the main areas where RMEP applies:
1. Building Codes and Energy Regulations
- Where: RMEP standards for buildings are often enforced by national or regional building codes and energy efficiency regulations.
- Example Locations:
- United States: Standards like the International Energy Conservation Code (IECC) set minimum energy performance levels for new residential and commercial buildings.
- European Union: The EU Energy Performance of Buildings Directive (EPBD) mandates that buildings meet certain energy performance standards for construction, renovation, and operation.
- Canada: The National Energy Code of Canada for Buildings (NECB) sets minimum energy performance requirements for new buildings.
- Australia: The National Construction Code (NCC) sets energy efficiency requirements for building design and construction.
- Why: These codes and regulations ensure that new buildings and major renovations meet energy-saving requirements, improving efficiency, reducing energy use, and contributing to sustainability goals.
2. Appliance and Product Standards
- Where: RMEP standards for consumer products and appliances are regulated by governmental bodies in many countries. These standards are typically enforced through labeling programs and regulations.
- Example Locations:
- United States: The Department of Energy (DOE) sets energy efficiency standards for appliances and other consumer products. For example, the Energy Star program certifies appliances that meet high energy efficiency standards.
- European Union: The EU has mandatory energy efficiency labeling for appliances under the Energy Labelling Regulation. Products such as refrigerators, washing machines, and light bulbs must meet minimum efficiency levels.
- China: The China Energy Label indicates the energy efficiency of household appliances.
- Australia: The Energy Rating Label provides information on the energy performance of household products.
- Why: These standards aim to reduce energy consumption in households and businesses, promoting the use of energy-efficient products and appliances.
3. Industrial Equipment and Processes
- Where: RMEP standards also apply to industrial facilities and manufacturing processes, where energy consumption is high. These standards may be mandated by local energy regulators or international organizations.
- Example Locations:
- United States: Industrial equipment must meet energy performance standards set by the DOE or EPA.
- European Union: Directive 2009/125/EC establishes eco-design requirements for energy-related products, which apply to a range of industrial equipment.
- China: National standards for energy efficiency in industry are governed by the China National Institute of Standardization (CNIS).
- Why: These standards are intended to improve energy efficiency in manufacturing, reduce operational costs, and minimize environmental impact.
4. Government Buildings and Public Sector
- Where: In many countries, government buildings and public sector projects must meet the highest standards for energy performance as part of sustainability initiatives.
- Example Locations:
- United States: Federal buildings must meet energy efficiency standards under the Energy Independence and Security Act (EISA), which includes compliance with Deming Rating or other energy certifications.
- United Kingdom: Public buildings must comply with the Building Regulations Part L, which set minimum energy performance standards.
- Canada: Government buildings must comply with the Federal Sustainable Development Strategy and Green Building Standards.
- Why: Governments often lead by example, ensuring that publicly funded buildings meet or exceed energy performance standards to promote sustainability and set an example for the private sector.
5. International Standards and Agreements
- Where: Many international agreements and standards guide energy efficiency across borders.
- Example Locations:
- Global: The International Energy Agency (IEA) promotes energy efficiency through initiatives such as the 3E+ (Energy Efficiency) Program, which helps countries set national energy efficiency policies.
- Paris Agreement: Countries that signed the Paris Agreement commit to improving energy efficiency and reducing emissions, indirectly influencing national RMEP regulations.
- Why: International standards and agreements drive the adoption of energy-efficient technologies, reduce global energy consumption, and help countries meet their sustainability goals.
6. Energy Performance Certificates
- Where: In many countries, buildings are required to have an Energy Performance Certificate (EPC) to indicate their energy efficiency level.
- Example Locations:
- European Union: Under the EPBD, all buildings sold or rented in EU member states must have an EPC showing their energy efficiency level.
- United Kingdom: An EPC is required for all residential properties that are sold or rented. It rates the building from A (most efficient) to G (least efficient).
- Australia: The NABERS (National Australian Built Environment Rating System) is used to assess the environmental impact and energy efficiency of buildings.
- Why: These certificates help building owners, tenants, and buyers understand a building’s energy efficiency, driving better decision-making regarding energy use and performance.
Conclusion:
RMEP standards are applied globally, with different rules and regulations depending on the location, whether for buildings, appliances, or industrial equipment. These standards are crucial for promoting energy efficiency, sustainability, and cost savings across various sectors.
How is Required Minimum Energy Performance
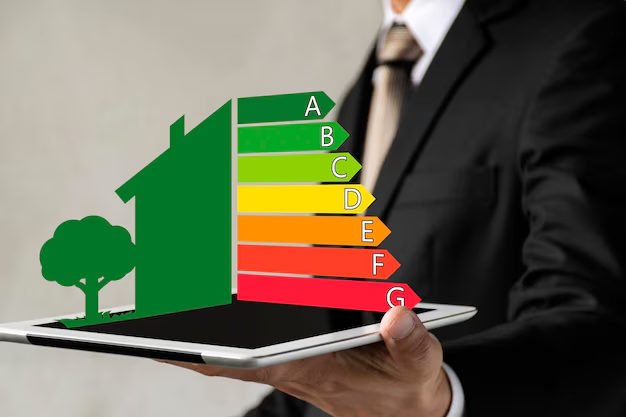
The Required Minimum Energy Performance (RMEP) standards are designed to ensure that buildings, appliances, systems, and equipment meet specific energy efficiency thresholds. These standards typically focus on minimizing energy consumption, lowering costs, and reducing environmental impact. Here’s how RMEP is implemented and maintained:
1. Through Codes and Regulations
- Building Codes: National, regional, or local building codes dictate the minimum energy performance required for new constructions and major renovations. These codes outline the energy efficiency standards for:
- Insulation: Requirements for wall, roof, and floor insulation to prevent energy loss.
- Windows: Standards for energy-efficient windows and glazing that limit heat loss or gain.
- Heating, Ventilation, and Air Conditioning (HVAC): Efficiency standards for HVAC systems to ensure they operate with minimal energy consumption.
- Lighting: Requirements for energy-efficient lighting systems, such as LEDs and automated controls.
- Example: In the U.S., the International Energy Conservation Code (IECC) sets the minimum energy efficiency standards for residential and commercial buildings, covering aspects like insulation, windows, and HVAC systems.
2. By Specifying Energy-Efficient Products and Systems
- Appliance Standards: Many products (e.g., refrigerators, air conditioners, water heaters, washing machines) must meet minimum energy efficiency standards set by government agencies, such as the U.S. Department of Energy (DOE) or the European Union. These standards limit the amount of energy that a product can consume during normal operation.
- Energy Labels: Products that meet these efficiency standards often carry an energy label, like the Energy Star label in the U.S. or the EU Energy Label. These labels provide consumers with clear information on the energy performance of the product.
- Example: A refrigerator in the U.S. must meet specific energy consumption requirements set by the DOE. If it meets the standards, it may be eligible for the Energy Star certification, indicating that it uses less energy than a conventional model.
3. By Integrating Energy Performance in Design and Construction
- Architectural and Engineering Design: During the design phase of buildings, architects and engineers incorporate energy-efficient elements, such as passive solar heating, high-performance insulation, and energy-efficient HVAC systems, to meet RMEP standards. This requires knowledge of energy modeling and simulation tools to design systems that meet the required performance.
- Energy Audits: Existing buildings may undergo energy audits to assess how well they perform energy-wise and identify areas for improvement. If a building does not meet the minimum required energy performance, it may need to implement upgrades (e.g., better insulation, more efficient HVAC systems).
4. By Setting Minimum Efficiency Thresholds for Energy Systems
- Renewable Energy Integration: Some RMEP regulations require the integration of renewable energy systems, such as solar panels or wind turbines, to meet energy consumption goals or to offset a building’s carbon footprint. The integration of renewable energy can be part of an overall strategy to meet or exceed RMEP standards.
- Energy Management Systems: In some industries, energy management systems (EMS) are implemented to continuously monitor and optimize energy use across operations. These systems help ensure compliance with energy efficiency standards.
5. Through Certification Programs and Rating Systems
- Energy Performance Certifications: Certification programs like Deming Rating are used to assess and certify buildings for energy performance. To achieve certification, buildings must meet a range of energy efficiency requirements, including insulation, HVAC efficiency, and overall building design.
- Example: A commercial building aiming for Deming Rating certification must demonstrate that it meets the energy performance criteria outlined by the U.S. Green Building Council, which includes reducing energy use by a certain percentage compared to baseline requirements.
6. Enforced Through Inspections, Audits, and Penalties
- Inspections and Compliance Checks: Authorities may conduct inspections or require documentation to confirm that a building or appliance meets RMEP standards. For instance, inspectors may verify that new homes meet energy performance requirements before occupancy.
- Penalties and Incentives: Failing to meet RMEP standards can result in penalties, fines, or the requirement to make costly retrofits. In some cases, there may also be incentives, such as tax credits or rebates, for exceeding minimum energy performance standards (e.g., for buildings with high levels of insulation or energy-efficient systems).
7. Ongoing Maintenance and Upgrades
- Building Upgrades: Over time, buildings may require upgrades to meet current energy efficiency standards. As technology improves, older buildings may fall behind the latest minimum energy performance thresholds. Regular upgrades or retrofitting, such as replacing old HVAC systems or insulating attic spaces, may be necessary.
- Energy Performance Monitoring: Energy performance should be monitored regularly in commercial and residential buildings to ensure that systems are functioning efficiently. Automated systems or energy management software may be used to optimize energy usage and identify inefficiencies.
How It Works in Practice:
- Example 1: New Construction: When constructing a new building, the architect and contractor will ensure that the design and materials comply with RMEP standards, such as using energy-efficient windows and installing a high-efficiency HVAC system.
- Example 2: Appliance Purchase: A consumer looking to buy a new air conditioning unit will check the Energy Star label to ensure that the unit meets the minimum energy performance requirements. The appliance will consume less energy than an older, less efficient model, which aligns with national energy conservation goals.
Summary:
The Required Minimum Energy Performance (RMEP) standards are enforced through building codes, appliance regulations, design requirements, and energy audits. They help ensure that buildings, appliances, and systems operate at efficient energy levels, reducing overall consumption and environmental impact. This is achieved through strict guidelines on construction, product manufacturing, and operation, enforced by government regulations, industry standards, and certification programs.
Case Study on Minimum Energy Performance
Retrofit of a Commercial Building
Project Overview: A commercial office building in Chicago, Illinois, built in the 1990s, was undergoing a major renovation. The building had outdated heating, ventilation, and air conditioning (HVAC) systems, poorly insulated windows, and inadequate lighting systems. The owner decided to undertake an energy efficiency retrofit to improve the building’s energy performance, reduce operating costs, and meet Required Minimum Energy Performance (RMEP) standards.
The project aimed to achieve compliance with local energy codes, including the Illinois Energy Conservation Code (IECC), and to improve the building’s overall energy efficiency to meet the Deming Rating certification for energy performance.
Objectives:
- Upgrade the building’s systems to comply with the latest energy efficiency standards.
- Reduce the building’s energy consumption by 30%.
- Achieve at least Deming Rating Gold certification for energy performance.
- Lower operating costs for the building tenants through energy-efficient improvements.
Steps Taken:
1. Energy Audit and Baseline Analysis
Before the retrofit began, a comprehensive energy audit was conducted to identify inefficiencies. The audit found several areas where the building failed to meet current energy standards:
- HVAC System: Outdated and inefficient, resulting in high energy use.
- Lighting: Fluorescent lights that were not energy-efficient and had manual controls.
- Windows and Insulation: Single-glazed windows with poor insulation, leading to heat loss in the winter and excessive heat gain in the summer.
The baseline energy performance of the building was measured, and a Energy Performance Index (EPI) was calculated to determine the gap between current performance and the target RMEP standards.
2. Design and Planning Phase
The project team (including architects, engineers, and energy consultants) worked to design the building’s upgrades with the following goals:
- Energy Efficient Windows: Replace single-glazed windows with double-glazed, low-emissivity (low-e) windows, which would significantly reduce heating and cooling energy demands.
- LED Lighting: Replace all fluorescent lighting with LED fixtures and install automated lighting controls (motion sensors, timers) to reduce unnecessary lighting use.
- New HVAC System: Install a modern, energy-efficient HVAC system with advanced features such as variable refrigerant flow (VRF) and demand-controlled ventilation to ensure optimal air quality and energy use.
- Insulation and Sealing: Upgrade insulation in walls, ceilings, and floors and seal all air leaks around windows and doors to improve thermal performance.
- Building Envelope: Enhance the overall building envelope to reduce heat transfer and improve the building’s overall energy efficiency.
3. Implementation
Once the design was approved, the retrofit work began, including the following key actions:
- HVAC System Replacement: The old HVAC system was replaced with a high-efficiency VRF system, which adjusts the temperature based on real-time demand. This reduced energy consumption by eliminating the need for constant heating and cooling.
- Window Replacement: All windows were replaced with double-glazed windows and treated with low-e coatings to reduce heat loss in winter and solar heat gain in summer.
- Lighting Upgrade: All lights were replaced with LED fixtures, which use at least 75% less energy than fluorescent lights. Additionally, motion sensors and automated dimming systems were added to minimize energy use when rooms are not in use.
- Additional Insulation: Spray foam insulation was added to walls and ceilings, and the building’s air barrier was sealed to prevent air leaks.
- Solar Panels: As part of the project, the roof was upgraded to accommodate solar panels. These panels would offset the building’s energy consumption, further reducing its environmental impact.
4. Performance Monitoring and Verification
After the retrofit was complete, energy performance was closely monitored to ensure that the building was meeting the new minimum energy performance standards:
- Energy Monitoring Systems: The building was equipped with smart meters and energy management software to track energy use across different systems (HVAC, lighting, etc.) and optimize performance in real time.
- Post-Retrofit Energy Audit: A second energy audit was conducted to verify that the building’s energy use had been reduced by at least 30% compared to the baseline.
- Verification of Deming Rating Certification: The building was reviewed by the U.S. Green Building Council (USGBC) to confirm it met the required criteria for Deming Rating Gold certification, including energy performance, sustainable materials, and indoor environmental quality.
Outcomes:
- Energy Savings:
- The building achieved a 30% reduction in energy use compared to its pre-retrofit consumption. The new HVAC system contributed to a significant decrease in energy used for heating and cooling, while the upgraded LED lighting and solar panels provided additional savings.
- The energy performance index (EPI) improved dramatically, meeting and exceeding the Illinois Energy Conservation Code (IECC) and Deming Rating Gold certification standards.
- Cost Savings:
- The building’s operating costs were reduced, particularly energy costs, due to the HVAC system upgrades, lighting changes, and better insulation.
- Tenants benefited from lower utility bills, which made the building more attractive to potential renters.
- Environmental Impact:
- The retrofit reduced the building’s carbon footprint by 40% due to decreased energy use and the integration of solar power.
- The building’s overall environmental impact was reduced, helping meet the city’s sustainability goals.
- Certification:
- The building was awarded Deming Rating Gold certification for its energy-efficient features, including the solar panel system, HVAC upgrades, and lighting retrofits.
Key Lessons Learned:
- Comprehensive Energy Audits Are Essential: Conducting thorough energy audits at the start of the project is crucial for understanding the baseline energy performance and identifying areas of improvement.
- Integrated Design is Key: Successful energy performance upgrades require collaboration among architects, engineers, contractors, and energy consultants to integrate energy-efficient solutions.
- Smart Technology for Monitoring and Optimization: Energy management systems and smart meters helped to continuously optimize energy use and track the building’s performance after the retrofit.
- Incentives and Grants: The building benefited from state-level incentives for energy-efficient retrofits, which offset a portion of the costs associated with the solar panels and HVAC system.
Conclusion:
This commercial building’s retrofit demonstrates how complying with Required Minimum Energy Performance (RMEP) standards can lead to significant energy savings, cost reductions, and environmental benefits. By following best practices in energy efficiency and integrating smart technologies, the building not only met the minimum energy performance requirements but exceeded them, achieving Deming Rating Gold certification and setting an example for future energy-efficient building renovations.
White paper on Minimum Energy Performance
Introduction
In today’s world, energy efficiency has become a cornerstone of sustainable development, contributing to significant cost savings, environmental protection, and reduced dependency on fossil fuels. Minimum Energy Performance (MEP) standards are regulatory requirements set by governments to ensure that buildings, appliances, and industrial equipment achieve a baseline level of energy efficiency. These standards are crucial for reducing energy consumption and mitigating the effects of climate change, making MEP an essential component of both energy policy and green building practices.
This white paper explores the concept of Minimum Energy Performance (MEP), its importance, implementation strategies, global trends, challenges, and future opportunities in the context of sustainability.
What is Minimum Energy Performance (MEP)?
Minimum Energy Performance refers to the set of requirements or standards that establish the least acceptable level of energy efficiency for buildings, appliances, industrial systems, and other energy-consuming equipment. These standards aim to reduce energy consumption, improve operational efficiency, and minimize the environmental impact of energy use.
Key Objectives of MEP:
- Reduce energy consumption: By setting energy performance thresholds, MEP ensures that new and existing buildings, products, and systems consume less energy.
- Lower operating costs: Efficient energy use reduces utility bills for owners, tenants, and businesses, contributing to cost savings over time.
- Promote environmental sustainability: Lower energy consumption reduces greenhouse gas emissions and the use of non-renewable energy sources.
- Compliance with regulations: Adhering to MEP standards ensures that buildings and equipment meet national, regional, or international environmental and energy efficiency regulations.
Why MEP Standards Are Crucial
1. Environmental Impact
- Climate Change Mitigation: The building sector accounts for nearly 40% of global energy consumption, with much of that energy coming from non-renewable sources like coal and natural gas. By enforcing MEP standards, governments can significantly reduce greenhouse gas emissions.
- Energy Resource Management: Efficient energy use helps manage limited energy resources, reducing reliance on fossil fuels and promoting renewable energy alternatives.
2. Economic Benefits
- Cost Savings: By improving the energy efficiency of buildings, appliances, and systems, MEP standards directly contribute to lower operational costs for businesses and homeowners.
- Increased Property Value: Energy-efficient buildings tend to have higher resale values and are more attractive to tenants, increasing demand for energy-efficient buildings.
- Job Creation: The shift toward energy-efficient technologies and building retrofits creates job opportunities in design, construction, and energy auditing industries.
3. Improved Quality of Life
- Health and Comfort: Energy-efficient buildings, particularly those with modern HVAC and lighting systems, improve indoor air quality and thermal comfort, contributing to healthier environments for occupants.
- Energy Security: By reducing overall energy demand, countries can better manage their energy resources and reduce dependence on imported fuels, enhancing energy security.
Implementation of MEP Standards
1. Energy Performance Codes and Regulations
MEP standards are typically embedded within national, regional, or local energy performance codes or building codes. These codes mandate that buildings meet specific energy consumption limits during construction, renovation, and operation.
Examples of Energy Performance Codes:
- International Energy Conservation Code (IECC) in the United States sets minimum energy performance standards for commercial and residential buildings.
- The Energy Performance of Buildings Directive (EPBD) in the European Union mandates that new buildings meet high energy efficiency standards, with renovations following suit.
2. Energy Star and Certification Programs
Many countries have energy labeling programs, such as the Energy Star program in the U.S., which helps consumers identify energy-efficient products and buildings. These programs not only set minimum energy performance thresholds but also incentivize higher performance with ratings or certifications like Deming Rating, BREEAM, and NABERS.
- Energy Star: A certification for appliances and buildings that meet strict energy efficiency standards.
- Deming Rating: A global green building certification program that rates buildings on a range of sustainability metrics, including energy performance.
- BREEAM: A widely recognized rating system for the environmental performance of buildings, focusing on energy use, emissions, and overall environmental impact.
3. Energy Audits and Retrofitting
Regular energy audits are conducted to assess the energy performance of existing buildings and identify areas for improvement. Audits typically include recommendations for retrofitting, such as improving insulation, upgrading HVAC systems, replacing outdated windows, and installing energy-efficient lighting.
- Retrofitting programs, such as Better Buildings in the U.S. or Energy Efficiency Obligation Schemes in the EU, provide financial incentives for building owners to upgrade their properties to meet modern MEP standards.
4. Monitoring and Verification
After implementing MEP standards, continuous monitoring is essential to ensure compliance. Technologies like smart meters and energy management systems (EMS) allow for real-time monitoring of energy use in buildings, making it easier to optimize performance and detect inefficiencies.
Global Trends in MEP Implementation
1. Stringent Regulations and Expanding Reach
Globally, MEP standards are becoming more stringent, and their scope is expanding to cover more areas of energy consumption:
- In the European Union, the Energy Efficiency Directive (EED) requires that the energy performance of existing buildings improves with each major renovation, and all new buildings must be “nearly zero-energy buildings” (NZEB) by 2020.
- The U.S. has seen growing adoption of the Energy Star program, with more residential and commercial buildings achieving certification.
2. Integration of Renewable Energy and Smart Technologies
The use of renewable energy (e.g., solar panels) and smart technologies (e.g., IoT sensors, building automation systems) is becoming more common in energy-efficient buildings. These technologies not only improve energy performance but also help buildings generate energy, offsetting their consumption.
3. Global Certification and Rating Systems
Global certification systems such as Deming Rating, BREEAM, and WELL are increasingly being adopted across countries, creating a more consistent and global approach to building energy performance.
4. Focus on Retrofits
Retrofitting older buildings to meet modern energy standards is becoming a priority, particularly in developed nations with large existing building stocks. Retrofits are often supported by government incentives, aiming to achieve broader energy efficiency goals.
Challenges in Implementing MEP Standards
- Upfront Costs: Implementing MEP standards, particularly in retrofitting buildings or replacing old appliances with more efficient alternatives, can be costly. However, these costs are often offset by long-term savings in energy bills.
- Technological Barriers: Some regions may lack access to the latest energy-efficient technologies, especially in developing countries.
- Lack of Awareness: Despite the benefits, some building owners or consumers may not be aware of MEP standards or the advantages of energy-efficient products, leading to slow adoption.
- Enforcement and Compliance: While many regions have MEP standards, ensuring compliance through inspections, audits, and penalties can be challenging, especially in less-regulated areas.
Future Opportunities
- Smart Cities and Urban Development: As cities grow, implementing MEP standards in new urban developments can help reduce the overall carbon footprint of cities.
- Energy as a Service: Offering energy performance improvements as a service, where third-party providers finance energy efficiency upgrades and share the savings, is an emerging model that can increase adoption.
- Advanced Technologies: The development of new materials, systems, and smart grids will continue to evolve and offer better ways to meet MEP standards with fewer trade-offs.
Conclusion
Minimum Energy Performance standards are essential for fostering sustainable energy use across various sectors. By setting clear performance thresholds for buildings, appliances, and industrial systems, these standards drive energy savings, reduce operational costs, and contribute to global efforts to combat climate change. Although challenges remain, the global trend toward stricter MEP regulations and the increasing integration of renewable energy and smart technologies indicate a positive trajectory for achieving energy efficiency goals worldwide.
This white paper provides an overview of the significance of MEP, its implementation strategies, and the future landscape of energy efficiency practices.
Industrial Application of Minimum Energy Performance
Courtesy: The Gambia Standards Bureau
Introduction
The industrial sector is one of the largest consumers of energy worldwide, responsible for a significant portion of global energy consumption and greenhouse gas emissions. As industries strive to reduce their environmental impact, cut operational costs, and improve their competitiveness, the adoption of Minimum Energy Performance (MEP) standards has become crucial. These standards help ensure that industrial operations, machinery, and processes meet minimum energy efficiency requirements, driving both economic and environmental benefits.
This section explores the industrial application of Minimum Energy Performance (MEP), focusing on its importance, implementation, key technologies, challenges, and the role of policies and regulations.
Importance of MEP in Industrial Settings
1. Energy Cost Reduction
- Operational Efficiency: The industrial sector often involves high energy-intensive processes, such as manufacturing, heating, cooling, and transportation. By adhering to MEP standards, industries can optimize energy use and reduce waste, leading to substantial cost savings in energy bills.
- Profitability: Energy-efficient processes can lower production costs, increasing overall profitability while maintaining competitive pricing in the market.
2. Environmental Impact
- Carbon Footprint Reduction: Industrial energy consumption is a major contributor to greenhouse gas emissions. Implementing MEP standards leads to less energy waste and helps industries reduce their carbon footprint, aligning with global sustainability goals.
- Compliance with Regulations: Industries must comply with increasingly stringent environmental regulations, including national and international energy efficiency standards. Meeting MEP standards ensures that businesses avoid potential fines or penalties related to non-compliance.
3. Enhanced Operational Performance
- Optimized Equipment Performance: Adhering to MEP standards often involves upgrading or replacing old equipment with more efficient machinery and systems. This results in improved operational performance, greater reliability, and reduced downtime.
- Increased Equipment Lifespan: Energy-efficient equipment tends to have a longer operational life due to reduced wear and tear, which ultimately lowers maintenance costs.
4. Access to Incentives and Financial Support
- Government Incentives: Many governments offer financial incentives, such as grants, subsidies, and tax rebates, for businesses that implement energy-saving measures. Complying with MEP standards increases eligibility for these incentives.
- Better Financing Opportunities: Energy-efficient projects are often viewed favorably by financial institutions, which may offer better financing terms to companies investing in energy-saving technologies.
Key Applications of MEP in Industrial Settings
1. Energy-Efficient Machinery and Equipment
- Motors and Drives: Industrial motors are a major source of energy consumption in manufacturing. By upgrading to high-efficiency motors and variable-speed drives, businesses can cut energy use significantly. MEP standards require the use of motors that meet specific efficiency levels, such as those certified by IEC (International Electrotechnical Commission) or NEMA (National Electrical Manufacturers Association).
- Pumps and Compressors: Pumps and air compressors are also energy-intensive components in many industrial settings. Ensuring that these systems meet minimum energy efficiency standards can reduce energy consumption and optimize performance.
- Lighting: Industrial lighting can represent a significant portion of a facility’s total energy usage. Replacing conventional lighting with LED fixtures and integrating occupancy sensors or daylight harvesting systems can lower energy consumption while maintaining appropriate lighting levels.
2. Energy Management Systems (EMS)
- Automation and Control: Energy Management Systems (EMS) enable real-time monitoring and control of energy use in industrial processes. By tracking energy consumption across different production areas, industries can identify inefficiencies, adjust processes, and optimize energy use. EMS systems often support the integration of Building Automation Systems (BAS), which manage both energy and building-related operations, such as heating, ventilation, and air conditioning (HVAC).
- Predictive Maintenance: Advanced EMS systems can predict when equipment is likely to malfunction or require maintenance, reducing downtime and energy waste associated with inefficient machinery.
3. Process Optimization
- Heat Recovery Systems: Many industrial processes, such as metal forging or chemical production, generate large amounts of waste heat. Heat recovery systems can capture this waste heat and use it to power other processes, such as preheating raw materials or generating steam. This contributes to improved energy efficiency and reduces reliance on external energy sources.
- Combined Heat and Power (CHP): CHP systems (also known as cogeneration) simultaneously generate electricity and useful heat from the same energy source, making them highly efficient. These systems meet MEP standards by improving energy utilization rates and reducing waste.
4. Industrial Insulation and Building Envelopes
- Thermal Insulation: Proper insulation of buildings and industrial equipment is essential to reduce heat loss or gain, particularly in energy-intensive industries such as petrochemical, food processing, and metal manufacturing. MEP standards often mandate specific levels of thermal insulation for buildings and industrial processes to prevent energy waste.
- Building Envelope Improvements: Sealing leaks in the building envelope, including walls, windows, and roofs, ensures that heating and cooling systems operate efficiently, reducing the need for excessive energy consumption.
5. Renewable Energy Integration
- Solar Power: Many industries are integrating solar photovoltaic (PV) systems to reduce energy dependence from external sources. By meeting MEP standards for energy efficiency and integrating renewable energy, industries can achieve a significant reduction in their energy bills.
- Wind and Biomass: In certain regions, industries are adopting small-scale wind turbines or biomass systems to generate renewable energy on-site. These technologies can reduce the reliance on grid power and contribute to meeting MEP standards.
Challenges in Implementing MEP in Industry
1. High Initial Investment
- Capital Costs: Upgrading equipment, installing energy-efficient systems, and adopting new technologies often require a significant initial investment. For smaller industries or companies with tight budgets, these upfront costs can be a barrier to adoption.
- Return on Investment (ROI): Although energy-efficient systems lead to long-term savings, the ROI period can sometimes be several years, which might deter businesses from making the necessary investment.
2. Lack of Awareness
- Many industrial operators may not fully understand the potential benefits of energy efficiency improvements or may be unaware of the available incentives and regulations. This can hinder the adoption of MEP standards.
3. Complexity of Retrofitting Existing Facilities
- Retrofitting older industrial facilities to meet MEP standards can be complex and disruptive. Existing buildings may not be designed for energy efficiency, and integrating new systems with older infrastructure can be challenging.
- Downtime during retrofits: In some cases, implementing energy-saving technologies requires temporarily halting production, which can affect business operations and profitability.
4. Technological Challenges
- Integration with Legacy Systems: Many industries still operate legacy systems that may not be compatible with modern energy-efficient technologies. Upgrading or replacing these systems may require additional resources and expertise.
- Data Management: Managing and analyzing large volumes of data from energy management systems can be challenging without the right tools or expertise, leading to missed opportunities for optimization.
Policy and Regulatory Support for MEP in Industry
1. Government Incentives
- Grants and Subsidies: Governments offer financial incentives such as grants, subsidies, and low-interest loans to help industries adopt energy-efficient technologies. These incentives can reduce the upfront costs of implementing MEP standards.
- Tax Breaks and Rebates: In some regions, businesses that invest in energy-efficient equipment or renewable energy systems may be eligible for tax credits or rebates.
2. Energy Efficiency Standards and Regulations
- Mandatory Energy Performance Standards: Many governments enforce MEP standards through legislation, requiring industries to comply with specific energy efficiency metrics for their operations, equipment, and facilities. Non-compliance can result in penalties or restrictions.
- Certification and Rating Systems: Industry sectors can also benefit from certification systems such as ISO 50001, which provides a framework for energy management and supports ongoing improvements in energy efficiency.
Conclusion
The industrial application of Minimum Energy Performance (MEP) standards is crucial for improving energy efficiency, reducing costs, and meeting environmental goals. By adopting MEP standards, industries can achieve long-term benefits such as lower energy consumption, reduced operational costs, and enhanced competitiveness. However, the implementation of MEP in industrial settings faces several challenges, including high initial costs, technological barriers, and the complexity of retrofitting older facilities.
Despite these challenges, the increasing availability of government incentives, technological innovations, and energy management tools provide significant opportunities for industries to improve their energy performance and contribute to global sustainability goals. Moving forward, industries must embrace energy-efficient technologies and systems to remain competitive and environmentally responsible.
References
- ^ Jaynes, E.T. (1968), p. 229.
- ^ Jaynes, E.T. (1979), pp. 30, 31, 40.
- ^ http://www.eceee.org S. Nadel S., 2003, Appliance & equipment efficiency standards in the US: Accomplishments, next steps and lessons learned, ECEEE 2003 Summer Study, St Raphael.
- ^ “energy jargon”. Archived from the original on 2008-07-19. Retrieved 2008-04-01.
- ^ Energy Efficiency in Brazil.[permanent dead link] Paulo Augusto Leonelli, Brazilian Ministry of Mines and energy. November 20, 2007
- ^ Energy Efficiency and Conservation Authority of New Zealand http://www.eeca.govt.nz/standards-and-ratings/minimum-energy-performance-standards-and-labelling
- Callen, Herbert B. (1985). Thermodynamics and an Introduction to Thermostatistics (2nd ed.). New York: John Wiley & Sons. ISBN 0-471-86256-8. OCLC 485487601